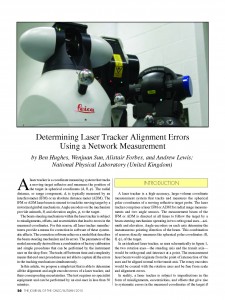
Download Members: $0.00 Non‑Members: $75.00 |
Buy Now |
Publication Details
Published Date: | |
---|---|
Authors: | Ben Hughes, Wenjuan Sun, Alistair Forbes, Andrew Lewis |
Company: | CMSC |
Print Format: | Technical Paper |
Citation: | Ben Hughes, Wenjuan Sun, Alistair Forbes, Andrew Lewis, "Determining Laser Tracker Alignment Errors Using a Network Measurement," The Journal of the CMSC, Vol. 5, No. 2, Autumn 2010 |
Abstract
A laser tracker is a coordinate measuring system that tracks a moving target reflector and measures the position of the target in spherical coordinates (d, ?, ?). The radial distance, or range component, d, is typically measured by an interferometer (IFM) or an absolute distance meter (ADM). The IFM or ADM laser beam is steered to track the moving target by a motorized gimbal mechanism. Angle encoders on the mechanism provide azimuth, ?, and elevation angles, ?, to the target. The beam-steering mechanism within the laser tracker is subject to misalignments, offsets, and eccentricities that lead to errors in the measured coordinates. For this reason, all laser tracker manufacturers provide a means for correction in software of these systematic effects. The correction software relies on a model that describes the beam-steering mechanism and its errors. The parameters of the model are usually derived from a combination of factory calibration and simple procedures that can be performed by the instrument user on the shop floor. The trade-off between time and complexity means that end-user procedures are not able to capture all the errors in the tracking mechanism simultaneously. In this article, we propose a simple test that is able to determine all the alignment and angle encoder errors of a laser tracker, and their corresponding uncertainties. The test requires no specialist equipment and can be performed by an end-user in less than thirty minutes.