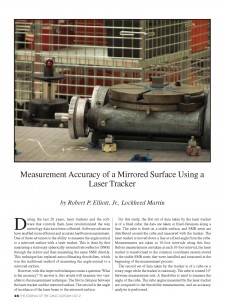
Download Members: $0.00 Non‑Members: $75.00 |
Buy Now |
Publication Details
Published Date: | |
---|---|
Authors: | Robert P. Elliott, Jr. |
Company: | CMSC |
Print Format: | Technical Paper |
Citation: | Robert P. Elliott, Jr., "Measurement Accuracy of a Mirrored Surface Using a Laser Tracker," The Journal of the CMSC, Vol. 7, No. 2, Autumn 2012 |
Abstract
During the last 20 years, laser trackers and the software that controls them have revolutionized the way metrology data have been collected. Software advances have enabled more efficient and accurate hardware measurement. One of these advances is the ability to measure the angle normal to a mirrored surface with a laser tracker. This is done by first measuring a stationary spherically mounted retroreflector (SMR) through the mirror and then measuring the same SMR directly. This technique has replaced autocollimating theodolites, which was the traditional method of measuring the angle normal to a mirrored surface. However, with this improved technique comes a question: What is the accuracy? To answer it, this article will examine two variables to the measurement technique. The first is distance between the laser tracker and the mirrored surface. The second is the angle of incidence of the laser beam to the mirrored surface. For this study, the first set of data taken by the laser tracker is of a fixed cube; the data are taken at fixed distances along a line. The cube is fixed on a stable surface, and SMR nests are distributed around the cube and measured with the tracker. The laser tracker is moved down a line at a fixed angle from the cube. Measurements are taken at 10-ft intervals along this line. Before measurements are taken at each 10-ft interval, the laser tracker is transformed to the common coordinate system stored in the stable SMR nests that were installed and measured at the beginning of the measurement process. The second set of data taken by the tracker is of a cube on a rotary stage while the tracker is stationary. The cube is rotated 10° between measurement sets. A theodolite is used to measure the angle of the cube. The cube angles measured by the laser tracker are compared to the theodolite measurements, and an accuracy analysis is performed. The goal of the study is to document the effect of distance and angle of incidence on mirrored surface measurement with a laser tracker.