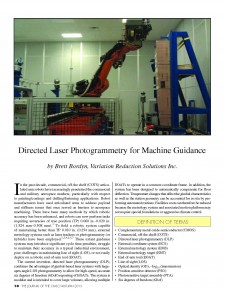
Download Members: $0.00 Non‑Members: $75.00 |
Buy Now |
Publication Details
Published Date: | |
---|---|
Authors: | Brett Bordyn |
Company: | CMSC |
Print Format: | Technical Paper |
Citation: | Brett Bordyn, "Directed Laser Photogrammetry for Machine Guidance," The Journal of the CMSC, Vol. 8, No. 2, Autumn 2013 |
Abstract
In the past decade, commercial off-the shelf (COTS) articulated arm robots have increasingly penetrated the commercial and military aerospace markets, particularly with respect to painting/coatings and drilling/fastening applications. Robot manufacturers have used articulated arms to address payload and stiffness issues that once served as barriers to aerospace machining. There have been many methods by which robotic accuracy has been enhanced, and robots can now perform tasks requiring accuracies of true position (TP) 0.060 in.–0.020 in. (1.524 mm–0.508 mm). To field a robotic system capable of maintaining better than TP 0.010 in. (0.254 mm), external metrology systems such as laser trackers or photogrammetry (or hybrids) have been employed. These extant guidance systems may introduce significant cycle time penalties, struggle to maintain their accuracy in a typical industrial environment, pose challenges in maintaining line of sight (LOS), or not easily deploy on a robotic end-of-arm tool (EOAT). The current invention, directed laser photogrammetry (DLP), combines the advantages of gimbal-based laser systems with large apex angle LOS photogrammetry in to allow for high-speed, accurate six degree of freedom (6DoF) reporting of EOATs. The system is modular, and is intended to cover large volumes, allowing multiple EOATs to operate in a common coordinate frame. In addition, the system has been designed to automatically compensate for floor deflection. Temperature changes that affect the gimbal characteristics as well as the station geometry can be accounted for in situ by performing automated routines. Facilities costs can therefore be reduced, because the metrology system and associated motion platform may not require special foundations or aggressive climate control.