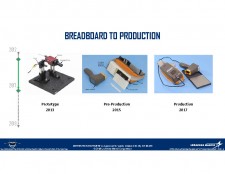
Download Members: $0.00 Non‑Members: $75.00 |
Buy Now |
Publication Details
Published Date: | |
---|---|
Citation: | Michael Allman†, David Novotny, Josh Gordon, Jeff R. Guerrieri |
Abstract
In this work, we describe the calibration of two robotic positioners that make up the Large Antenna Positioning System (LAPS) at the National Institute of Standards and Technology (NIST). NIST developed LAPS to support over-the-air (OTA) testing needs for modern communications systems in the commonly used bands between (0.5-30) GHz. Paramount to the performance of any OTA test facility is the ability to accurately position source and probe antennas over the scanning volume. A rule of thumb used in the antenna community is that the absolute accuracy of the positioners must be at least λ/50 where λ is the wavelength of the radiation pattern being measured. Thus, a system with a maximum operating frequency of 30 GHz requires a positioning accuracy of approximately 0.2mm.
The LAPS system, shown in Figure 1, consists of two kinematically-linked, Yaskawa† 6 axis serial robotic arms. To center the robots’ working volume in the optimal quite zone of the chamber, each robot is mounted on a pedestal. One of the robot pedestals is mounted on a 7m linear rail system while the other pedestal is fixed to the chamber floor. The moveable-base robot (MR) has a scan volume of approximately 5m(H) × 6m(W) × 10m(L). The stationary-base robot (SR) has a scan volume of approximately 4m(H) × 5m(W) × 2m(L). For a typical OTA measurement, a source antenna is mounted to the SR’s tool control point (TCP). A probe antenna is mounted to the MR’s TCP. The source antenna’s field pattern is then spatially digitized using the probe antenna. This digitized near-field data is then holographically transformed into the far field where crucial antenna parameters, such as gain and polarization, can be extracted. The spacing size and ability of the positioner to accurately reach these points determines the upper frequency limit the system is capable of measuring.
Previous work by NIST and others has shown that robots can be accurately positioned to within (0.025 - 0.050) mm using constant monitoring and correction by an external metrology system (EMS) such as a laser tracker [1, 2]. However, this added complexity reduces the flexibility that the LAPS system was intended to have. Alternatively, the accuracy can be improved to approximately 0.2 mm by calibrating the robot kinematic model [3]. This method only requires the use of the EMS for the calibration. Once the improved kinematic model parameters are updated in the controller, the EMS is no longer needed during data acquisition.
Our previous robot calibration work used an optimization routine embedded in our New River Kinematics Spatial Analyzer (SAMachine) Software†. However, the kinematic model used in SAMachine is based on classic Denevit-Hartenberg (DH) parameters whereas the model used in our robots’ controllers is based on modified DH parameters [4]. This difference motivated us to develop our own optimization program based on the open source Python library, SciPy. Our program incorporates both classic and modified DH parameter models, provides more flexibility in motion planning, allows faster code development and easier distribution to different systems at NIST. Once calibrated, the model was then validated by sampling over the interior of the calibration volume and comparing the nominal to the actual positioning. Positioning backlash was managed by giving each target position an approach position by subtracting a fixed number of pulse counts from each joint.