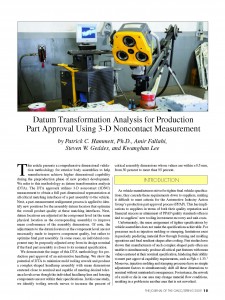
Download Members: $0.00 Non‑Members: $75.00 |
Buy Now |
Publication Details
Published Date: | |
---|---|
Authors: | Patrick C. Hammett, Amir Fallahi, Steven W. Geddes, Kwanghan Lee |
Company: | CMSC |
Print Format: | Technical Paper |
Citation: | Patrick C. Hammett, Amir Fallahi, Steven W. Geddes, Kwanghan Lee, "Datum Transformation Analysis for Production Part Approval Using 3D Noncontact Measurement," The Journal of the CMSC, Vol. 4, No. 1, Spring 2009 |
Abstract
This article presents a comprehensive dimensional validation methodology for exterior body assemblies to help manufacturers achieve higher dimensional capability during the preproduction phase of new product development. We refer to this methodology as datum transformation analysis (DTA). The DTA approach utilizes 3D noncontact (3DNC) measurement to obtain a full part dimensional representation at all critical matching interfaces of a part assembly to the vehicle. Next, a part measurement realignment process is applied to identify new positions for the assembly datum locators that optimize the overall product quality at these matching interfaces. Next, datum locations are adjusted at the component level (at the same physical location as the corresponding assembly) to improve mean conformance of the assembly dimensions. Of note, the adjustments to the datum locators at the component level are not necessarily made to improve component quality, but rather to optimize final part assembly. In some cases, an individual component may be purposely adjusted away from its design nominal if the final part assembly is closer to its nominal specification. We demonstrate the usage of this DTA methodology for production part approval of an automotive headlamp. We show the potential of DTA to minimize mold tooling rework and produce a complex-shaped headlamp assembly with mean dimensions centered close to nominal and capable of meeting desired tolerance levels even though the individual headlamp lens and housing components are not within their specifications. In this case study, we identify tooling rework moves to increase the percent of critical assembly dimensions whose values are within ± 0.5 mm from 50 percent to more than 95 percent.