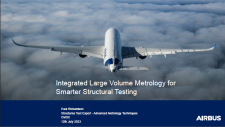
Download Members: $0.00 Non‑Members: $75.00 |
Buy Now |
Publication Details
Published Date: | |
---|---|
Authors: | Paul Richardson |
Download Format: |
Abstract
Smarter Testing is an Aerospace Technology Institute (ATI) funded project led by Airbus, with project partners Dassault Systemes, NPL, Zeiss and CFMS. It focusses on 5 areas: A Data Driven Platform, Advanced Measurement Technologies, Advanced Quantitative Data Correlation, Advanced Data Analytics and Test Optimisation. The Advanced Measurement Technologies work package considers some of the challenges of Integrated Measurements in a large volume test environment, and attempts to solve them. One of the biggest challenges is the difference in scales and granularity of the measurements required. The results are typically used for the validation of finite element modelling and this can appear at different scales. It can be of a fairly low resolution global FE model of a full-scale aircraft component, requiring overall deflection measurements at above millimetre accuracy. At the other extreme it can be a very local, detailed, Non-Linear FE model covering a small, sub-metre volume and requiring measurement at sub-millimetre (100 or 10 micron) accuracy. These differences of scale and accuracy require different measurement systems individually configured and calibrated to the specific measurement volumes.
The physical logistics of a large scale test rig can present challenges of access to physically install measurement devices, and block lines of sight for optical measurement techniques. These physical constraints can also change as the test proceeds and large deflections of structures are encountered. The access available can also determine the measurement technique used, depending on the necessary sensors, targets, reflectors, coating or patterns required, as well as fields of view and equipment stand-offs available.
The measurement of different parameters (both geometric and structural) also require different metrology technologies to be used and these have typically been stand-alone measurement systems and not all linked together into one central system. By investigating the use of common targeting, common reference systems and common time-stamping we intend to bring all these data sets into a common coordinate system and process in a single data platform to enable like-for-like comparison with the simulation and modelling.
The final challenge is to integrate the end-to-end process in this single data platform, from definition of the measurement requirements through to post-processing and comparison of the data. This will also include the use of both live and post-processed monitoring to identify test specimen behaviours, to protect the test against premature failures and to reduce down-time by employing condition-led inspections.