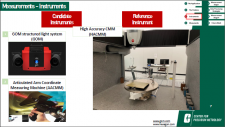
Download Members: $0.00 Non‑Members: $75.00 |
Buy Now |
Publication Details
Published Date: | |
---|---|
Authors: | Rehab Khattab, Dr. Edward Morse |
Download Format: |
Abstract
Various large-scale metrology tools have proven their worth in measuring aircraft (and other) components whose size is measured in tens of meters. The primary output of these measurements is geometry data, such as cross-sectional profiles, the shape of cutouts, or the location of assembly points. The work described here relates to characterizing the location and orientation of smaller features (holes) as part of these larger measurements.
The purpose of these measurements is to allow the machining of holes on a mating part for joining. Historically, a technique called "match drilling" is used to be certain that the fastener holes on a pair of parts are aligned. However, this technique can be awkward for complex part geometries, and the manual nature of the process is time consuming. If the hole location and orientation can be captured with sufficient accuracy on the first part, the drilling of the second part can be done using a CNC machine.
The work described in this paper investigates both contact and non-contact measurements for the drilled holes, and compares the repeatability of the methods as well as agreement to reference measurements performed with a high-accuracy CMM.
To begin the measurement process, two primary instruments were used to scan Part A: the GOM Structured Light System and the Articulated Arm CMM. The primary goal of this stage of measurements is to assess the repeatability of the primary measurements. By comparing these measurements with reference data, an initial bias can also be determined. This first stage is crucial for establishing a foundation for the subsequent stage of measurement.
The first stage of measurement provided the initial assessment of the repeatability and bias of the primary measurements. Following this, the second stage involved optimizing these primary measurements. To achieve this, all factors that may affect the primary data were identified and defined. Based on these factors, a measurement strategy is developed to ensure the most accurate data was obtained. The optimization process builds upon the foundation established in the first stage and aims to refine the measurement process for improved precision and accuracy up to 25 μm.
The initial factor involved in the process is reliant upon extracting the intricate features from the scans. Typically, the equipment used generates point cloud data. Once this data has undergone pre-processing to eliminate noise, outliers, and other artifacts that could impede feature detection, various algorithms can be used to identify the features of interest. A range of techniques were employed to extract features from the output point clouds and compared against each other to determine the optimal method for accurately extracting the detailed features.
The subsequent factors relate to the measurement parameters, which include those associated with different instruments and those within each instrument. A variety of measurement sets were collected, with each set possessing specific parameters. Some examples of these parameters that may vary between the sets include (but not limited to) the angle of the instrument relative to the test part, the location and number of reference points, and the type of measurement tool used (contact vs. non-contact). Additionally, segmentation-related parameters may also be modified to optimize the measurement process.
Once the optimized primary measurements are obtained, they are compared to the reference measurement obtained from the high accuracy CMM to determine the bias. Subsequently, uncertainty tests and analyses are performed to identify the most precise and accurate measurement strategy among the primary measurement strategies.